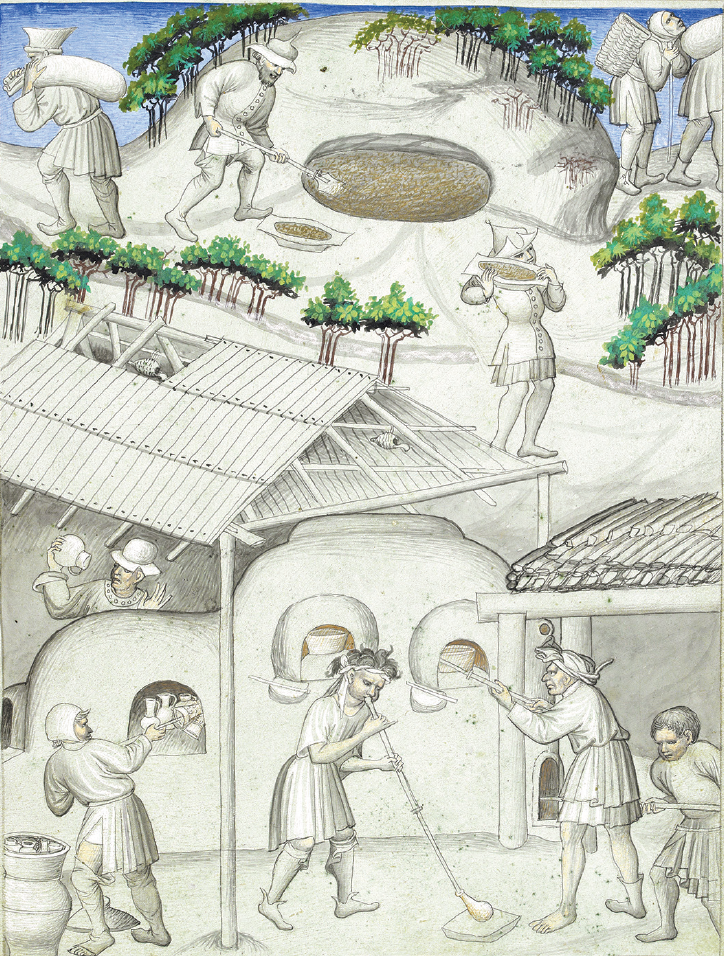
The Hive of Activity at the ‘Glasshouse’ 1585-7 – a Window on the Development of Knole
Contributions to the next volume are welcome. See the guidance for contributors and contact Editor Jason Mazzocchi. Also see the guidance for peer review.
Search page
Search within this page here, search the collection page or search the website.
Playing the Passion in late fifteenth-century New Romney: the Playwardens’ Account Fragment
The Kentish Demonym – or, the Demonym of Kent
The Hive of Activity at the ‘Glasshouse’ 1585-7 – a Window on the Development of Knole
Stephen Draper
137
The Hive of Activity at the ‘Glasshouse’ 1585-7 – a
Window on the Development of Knole
stephen draper
In Elizabethan times ‘glasshouse’ denoted a large, temporary structure
covering the furnaces and work areas necessary for making glass. John
Lennard, a wealthy Bencher of Lincoln’s Inn, was the tenant of Knole (owned
by the Crown) from 1570 to 1590 during which time he undertook huge
restoration. This included reglazing the house for which a very substantial
manufacturing facility on site was required.
A wealth of correspondence between Lennard in London and his steward
at Knole detailing the progress of glass production during 1585-7 has
survived. This is summarised below together with a brief description of the
techniques of glass production at the period, the materials required and the
Continental origins of the itinerant ‘glassmen’.
Knole is a very large house, with a ground-plan area of buildings of 4.4 acres,
arranged around seven courtyards (Fig. 1); there is a walled garden of 26 acres, set
Fig. 1 ‘Knole, more like a town than a house’, Virginia Woolf Orlando.
(Photo by S. Draper.)
STEPHEN DRAPER
138
in a Park of 1,000 acres. Since the Park was created in about 1460 it has roughly
doubled in size. There has been very little disturbance to the land after being
brought within the paling. The house itself has been subject to several building,
restoration and improvement projects.
John Lennard, tenant of Knole, had chambers in Lincoln’s Inn because of his
legal work. He was a Bencher at Lincoln’s Inn and had been called to the bar, but
under a special procedure as he was a court administrator. He held various roles in
the Court of Common Pleas, gaining influence and money as his responsibilities
increased. Thus, when Wales was divided into shire counties, Lennard set up the
court system there, for which Edward VI awarded him a standing fee and enlarged
his letters patent – allowing Lennard opportunities to get richer. When the post of
Custos Brevium (Keeper of Writs) of the Court of Common Pleas became available,
Lennard was able to pay the rights holder, Sir William Cecil, an annuity of £240
for the post.1 In the early 20th century, Lennard’s family historian, Thomas Barrett
Lennard, studied John’s web of leases and properties bought and sold, and other
business dealings and accounts, and reckoned John to have had an annual income
of £2,000.2
As Lennard was often at Lincoln’s Inn, many estate matters that would normally
have been reported verbally were written down. That is why the glasshouse at
Knole is the best-documented glasshouse of its period. Lennard’s original
documents referred to in this paper (and hundreds more) are in the County Archives
in Maidstone and Chelmsford. Transcripts of some were published by Thomas
Barrett Lennard in 19053 and 1908.4
Lennard’s lease of Knole had been taken over from Thomas Rolf four years
after Rolf’s death in autumn 1566.5 Earlier, in 1561, the Earl of Leicester had
commissioned a survey of Knole which detailed its ruinous state.6 Rolf’s lease7
required the Crown to repair Knole and allowed its tenant to make changes to the
house.
Before taking over the residue of the lease in 1570, Lennard commissioned his
own survey which valued the necessary restoration work at £304 5s. 5d. [£900k]
and a covenant was put in place that the Crown would do the work. However, by
1587 the Crown had done nothing, deterioration had continued and Lennard had
himself now undertaken all that was necessary. He wrote that ‘I will take my oath
before you that I have laid out in repairing it standing with the covenant £400
& more, besides stone walling the house, & garden, & other voluntary acts for
the which I ask no thing’. The Chancellor, on behalf of the Crown, had offered
Lennard too little money, and Lennard was not prepared to release the Crown
from the covenant. He asked Lord Burghley to rebate his rent by £400 [£1.2M]
(i.e. two years free), or to reduce the annual rental by double the Chancellor’s
offer. He commented that he had saved the Crown money by doing the repairs
over the 15 years of his tenancy: ‘if it had not been done in time but let go, £1000
[£3M] would not now have done it’. Lennard also notes that he has developed
the estate. Lennard’s statement that he had spent, on his own account, large sums
on ‘stone walling the house and garden’ is very significant for our understanding
of the development of Knole House.8 If the stonewalling of the house refers to
significant work on Green Court, this would make sense.
Lennard spent a lot of money on having window glass made in the late 1580s.
THE HIVE OF ACTIVITY AT THE ‘GLASSHOUSE’ 1585-7 – DEVELOPMENT AT KNOLE
139
The wood recorded as supplied to the glassmen was valued at today’s equivalent
of £517,000. He had a lot of windows to put it in, and we find window glass of the
right type and period in many of the leaded diamond windows on the inner and
outer walls of Green Court.
In the following sections some aspects of making window glass in England at the
period are explored, the manufacturing process described and Lennard’s unique
and detailed records of the Knole glasshouse operations summarised.
Quality problems of English window glass
The best English window glass in the Medieval period came from the Weald of
Surrey and Sussex, and from Shropshire and Staffordshire. In 1351 and 1355 white
glass from Chiddingfold, near the Surrey/Sussex border, was used for the glazing
of St Stephen’s Chapel, Westminster, and for the new chapel at Windsor Castle.9
From the Medieval period onwards, Chiddingfold was one of the foremost English
locations for glassmaking. In addition to documentary records of glassmaking, the
remains of a number of furnaces from different periods have been found there.10
The places favoured by the glassmakers were wooded, low and with water nearby
– to the point of being boggy. There is a source of white sand very nearby at
Hambledon.11
However, English glass was often considered inferior.12 Window glass from
Normandy was considered superior to English and other foreign glasses, and
fetched the highest price. Indeed, in 1567 the master of a glasshouse at Chiddingfold
claimed that he could not make window glass, only ‘bottles and other small
wares’.13 The problems with making sheet glass were well known, and foreign
experts had presented themselves to the Crown to offer a solution.
Lord Burghley favoured the application from a Huguenot glassmaker, Jean Carré
of Arras, to pay the Crown for a monopoly on glassmaking.14 In 1567 his company
gained 21-year rights in making window glass, with conditions on pricing and the
training of English glassmakers. From 1570 Carré brought a number of French and
Venetian glassmakers into the country and, in spite of a number of complications
with the commercial arrangements, and Carré’s death, glasshouses were built and
began to produce window glass of a very high quality.
Production continued, making the now-fashionable large windows for the
great houses, and devouring wood at a rate which began to threaten the vital
iron industry. The solution was to adapt the process to use coal, which allowed
even higher furnace temperatures and better glass to be made.15 A monopoly was
granted in 1615 and the use of wood for the so-called Forest Glass was banned and
had ceased by 1620. Many of the Huguenot glassmakers had moved to places like
Staffordshire, where the forests had allowed a glass industry to develop, but where
coal was also available, enabling the industry to modernise.
Technique of making Forest Glass
Forest glass made between the arrival of Carré in 1570 and its final demise in 1620
is known as Late Period glass. The manufacture of large quantities of glass took
place in the forests for the simple reason that a lot of wood was used in the process
STEPHEN DRAPER
140
Fig. 2 A medieval ‘glasshouse’; drawing made in Bohemia c.1420. Men are collecting
wood, sand and vegetation to make the ash. There is a shingled roof over the furnace,
and a much stronger structure on which furnace wood is drying. (Reproduced, with
permission © British Library Board Add. MS 24189-f016r.)
THE HIVE OF ACTIVITY AT THE ‘GLASSHOUSE’ 1585-7 – DEVELOPMENT AT KNOLE
141
in the form of ash and fuel. Sand was used, but does not melt and fuse into glass
at the temperatures that can be obtained in a furnace. All glass requires an alkaline
‘flux’ that reacts with the sand to help it to melt. That flux could be soda – making
high-quality soda glass – potash or lime. For making fine glass vessels the ash
was often refined to extract the alkali in concentrated form. Unrefined wood ash
contained a mix of minerals that made more robust, green glass and this is what
was generally made in England.
The Late forest glass was clearer, stronger and weathered better than anything
previously made in England. Fourteenth-century window glass had to be at least
3/16in. thick, which required very strong window structures. Late Glass could be
made to 1/16in. or less, and be readily cut into diamond ‘quarries’ and mounted
in a lead matrix.16 This improvement was achieved by higher and more constant
temperatures from improved furnace design, and by raising the calcium content by
burning wood that contained more lime, i.e. oak rather than beech, or possibly the
secret was to add lime itself.
The basic recipe for glass required two parts by weight of ash and one of sand.
If the furnace was burning the right wood, its own-derived ash could be used. The
efficient, high temperature, Late Glass furnaces could make a unit of glass with
only 100 units of wood. Earlier glassmaking required 200 units of wood. In either
case only 1 unit of sand went into every 3 units of glass.
For centuries, glassmakers had used a 3-chamber process to make the glass. All
access to the working areas of the furnace took place through apertures made as
small as possible to retain heat. Long ladles, stirrers and other tools were used
to reach the working pots inside the furnace (Figs 2 and 3). The furnace is the
centre of activity, starting from the right, a boy is stoking the furnace. In the first
chamber, held at 900°C,17 the founder has put the ingredients into a pre-heated
pot. Once it started to melt, the mixture had to be stirred continuously, for a day
and a night, until it had consolidated into ‘frit’. The frit was ladled into one of
the working vessels in the main furnace, kept at about 1300°C. Each side of the
working furnace had two pots, one having frit added to it and forming glass, the
other having glass taken out, blown and worked. The final stage took place in the
annealing furnace, where the finished glass was first heated to 900°C, then cooled
over a day. This allowed the tensions in the glass to be released without any loss
of form.
All wood-fired furnaces were reverberatory, they relied on confining the heat
inside and maintaining temperature for months at a time so that all the structure,
interior shelves and pots were maintained at the working temperature. Late furnaces
were constructed from a sandy stone with an outer shell of neat brickwork or stone,
at least 30cm thick in total. The top corners were curved so that there were no cold
spots and the maximum heat was reflected down into the pots. Brick could not be
used for the lining because it would have become glass, and melted. Inside the
furnace the pots stood on a shelf which had circular indentations so the pots were
kept in place during stirring. Finding suitable clay for the pots, and making pots
that would withstand the heat, had been a major issue before the Late Period. Good
Green glass required an extra-hot furnace: one glassmaker remarked that it was
twice as hot for the workers as when making other types of glass.18 Pipe clay from
sites such as Purbeck was mixed with fire clay from Worcestershire or the Forest of
STEPHEN DRAPER
142
Dean to make a strong and resistant pot.19 Late pots were usually large, often tapered
bucket shapes, 30 cm diameter at the base, 35-38 cm at the top and 30-40cm high.
The walls were 2-2.5 cm thick and the base 5cm, although some Late pots have been
found with walls only 1.5 cm thick.20 A full pot would hold about 75kg of glass.
The furnace had to have an aperture big enough to allow pots to be changed, and
which could be much reduced in size to keep in the heat. This was done with a plug
of clay shaped on a frame of sticks and with a ‘glory hole’ just big enough to allow
insertion of ladles, pipes, etc. This plug baked in place and the sticks burned away.
It would be removed for pot changing and replaced if it broke.
Ash from different woods has different amounts of sodium, potassium and
calcium, and made glasses with different characteristics. Oak, for example, has
much higher levels of calcium than beech, so should make glass that weathers
better. However, there can be huge variations between batches of ash.
The founder made his frit in batches which consolidated to a smaller volume,
and then added it to the ‘metal’ in the main furnace to form glass. There was
much testing: tasting to check the alkalinity,21 and pouring to check the viscosity
and quality of the product. He could use, for example, a different sort of ash
for one portion of frit to adjust the quality of the metal. It had to have the right
characteristics to be blown into good window glass.
Fig. 3 Drawings of glassmens’ tools. (Reproduced from Jean Haudicquer de Blancourt,
The Art of Glass, First translated into English (London, 1699), p. 32. From